not approved
Building Affordable Houses Quickly
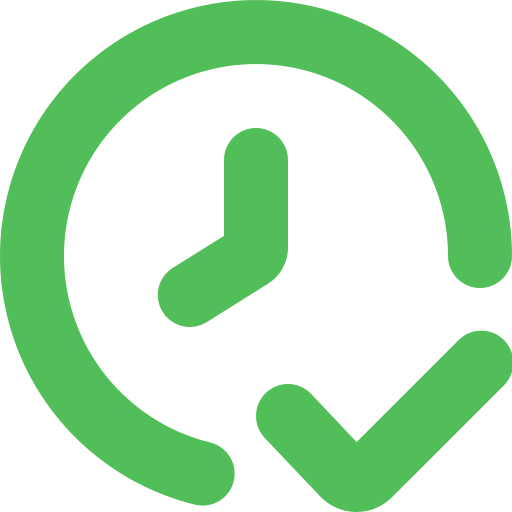
Current Project Status
Unfunded
Amount
Received
Received
$0
Amount
Requested
Requested
$68,000
Percentage
Received
Received
0.00%
Solution
TBA
Problem
Addresses Challenge
Feasibility
Auditability
Building Affordable Houses Quickly